Body Damage
Body damage to items such as your car are not something we expect to happen but can nevertheless happen to anyone.
If the damage is not too great, most people can repair it by themselves with a little time and patience.
What kinds of putty are there?
Hand putty is usually a two-comp polyester putty, acrylic or cellulose putty.
When it comes to hand putty there are all-round and fine putties. All-round putty (filler) is used for filling larger areas, while fine putty or glazing putty is for filling smaller areas. The closer it is to the lacquer, the finer (tighter) should be the putty.
Spray putty can be 2-comp and polyester-based or 1-comp acrylic-based.
Step 1
Begin by cleaning the surface to be repaired and the area around it with silicon removal, thinner or some other solvent which is not greasy. Then dry with a clean, soft rag. |
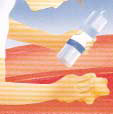 |
Step 2
If it is normal chassis sheet metal that is being repaired, sand lightly with sandpaper. If the surface area is large, you can use a sander. A suitable sandpaper is 80-grit. Any rust must be removed. If the rust is not carefully removed, new rust will develop. Sand the joints between the repair area and the surrounding layer of lacquer using 180-grit sandpaper, so that the surface becomes as even and smooth as possible. NOTE: If it is galvanised sheet metal being repaired, sand only the surface lightly using fine sandpaper, such as a 240-grit. This will not damage the galvanisation. Any rust on the surface must be removed. Sand using an 80-grit sandpaper. If the substrate is pure aluminium, degrease the surface first with silicon removal, then sand the surface lightly using P 180-240 fine-grit sandpaper and degrease the surface once again.
Prime the aluminium surface with a 2-comp epoxy primer, Hagmans Base Primer CA in a thin coat, 10-15 wet my. Let it dry for as many minutes as the amount of applied my, before applying the putty. |
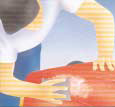 |
Step 3
After this has dried, dry off any sanding dust with a tack rag or another napp-free rag. |
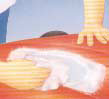 |
Step 4
Then mix the suitable steel plastic product on something such as a board or a pane of glass. All our products are 2-compent polyester spackling agents. Do not mix more at one time than you can use within 4-5 minutes as the putty will quickly stiffen after mixing.
Take a useable amount of composite A from the tin and add 2-3% hardener (composite B, from the tube). Mix thoroughly until the mixture has a consistent colour. This is important. |
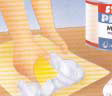 |
Step 5
Use a steel or rubber spatula or putty knife when working with the putty. If the dent (the damaged area) is more than 3-4mm deep, you should apply the putty in stages, i.e. putty, sand, putty, and sand. This will assure you of the perfect end result. |
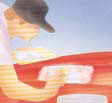 |
Step 6
When the putty has hardened (this will take 15-20 minutes), sand first with 120-grit dry sandpaper. To avoid scratching the bodywork, follow this up with a finer paper such as a 180-grit paper.
Then finish off with 320-grit sandpaper. Use a sanding block when sanding. |
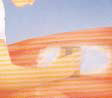 |
Step 7
If you paint directly on top of the putty, blisters in the lacquer layer and a matte topcoat may result. Therefore, apply a base primer first, such as a 1-Comp Anticorrosion Primer, red (spray), Hagmans Base Primer Grey (spray) or Spray-Max Filler Primer (spray) after you have protected the surrounding surface with protective paper. When the primer has dried over the course of 15-20 minutes, apply Steel Plastic Spray Putty or Spray Max Acrylic Filler, if you want the very best result. |
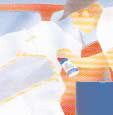 |
Step 8
After about thirty minutes, sand the spray putty lightly using a 1000-grit or finer wet sandpaper. |
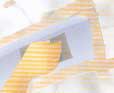 |
Step 9
Wash once more using silicone removal (use a soft, clean cloth). |
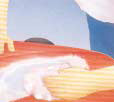 |
Step 10
After this, you dry the area with a tack rag and apply the topcoat. Be sure to follow the manufacturer’s directions. |
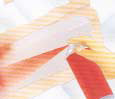 |
Golden rules
- Always be thorough with preparatory work.
- Always follow instructions for the product.
- Always do your best to perform the work in surroundings with a room temperature of about 20°C and with normal humidity levels.
- Always ensure good ventilation levels.
- Always handle the products with care and use protective equipment.
|
Common problems
- Undoubtedly, the most common problem when building up a lacquer system is poor preparatory work which may result in poor adhesion, bubbles, blistering, dirt in the lacquer or finish, and rust.
- Poor anticorrosive primer or layers that are too thin can quickly lead to rust damage and loss of adhesion.
- Sandpaper that is too coarse will cause scratch marks that will be visible through the next coat of lacquer.
- Lacquering directly onto aluminium without relevant priming can lead to loss of adhesion and blistering. NOTE: On new aluminium it can, however, be very difficult to achieve a stable lacquer system. This is due to it being rolled with grease which results in a surface that is not ’open‘. The following work stages will improve adhesion: Degreaseing+grinding+degreasing.
- Poor feathering of edges and insufficient spackling, spray putty and/or filler will result in feathered edges and irregularities being visible through the topcoat.
- Quick putty and Spray Putty applied directly to bare steel plating may lead to blistering. The same applies for 2-component polyester-based Spray Putty 900.
- Variable factors such as applying the incorrect amount of hardener in a 2-componenet system, temperature, as well as humidity, will affect the curing time and the degree of hardening. Applying too much hardener in polyester putty may discolour the topcoat.
- An epoxy-based product does not harden sufficiently if the proportions between the A and B-components are incorrect. The drying time for a water-borne system is longer in high humidity conditions. A polyurethane system may lather if the humidity is too high or if it comes into contact with water.
- All kinds of systems harden/dry more quickly at higher temperatures. Make sure you read the relevant information on what applies for the system you are using.
|